For the final project of my metal machining class (called Metal II), I wanted to improve my skills by making something with interacting components. In the end, I completed 3 pens made with the same threads, allowing all components to be interchangeable. I bought a pack of gel pen refills and all pen components were designed and machined to accommodate the refills precisely.
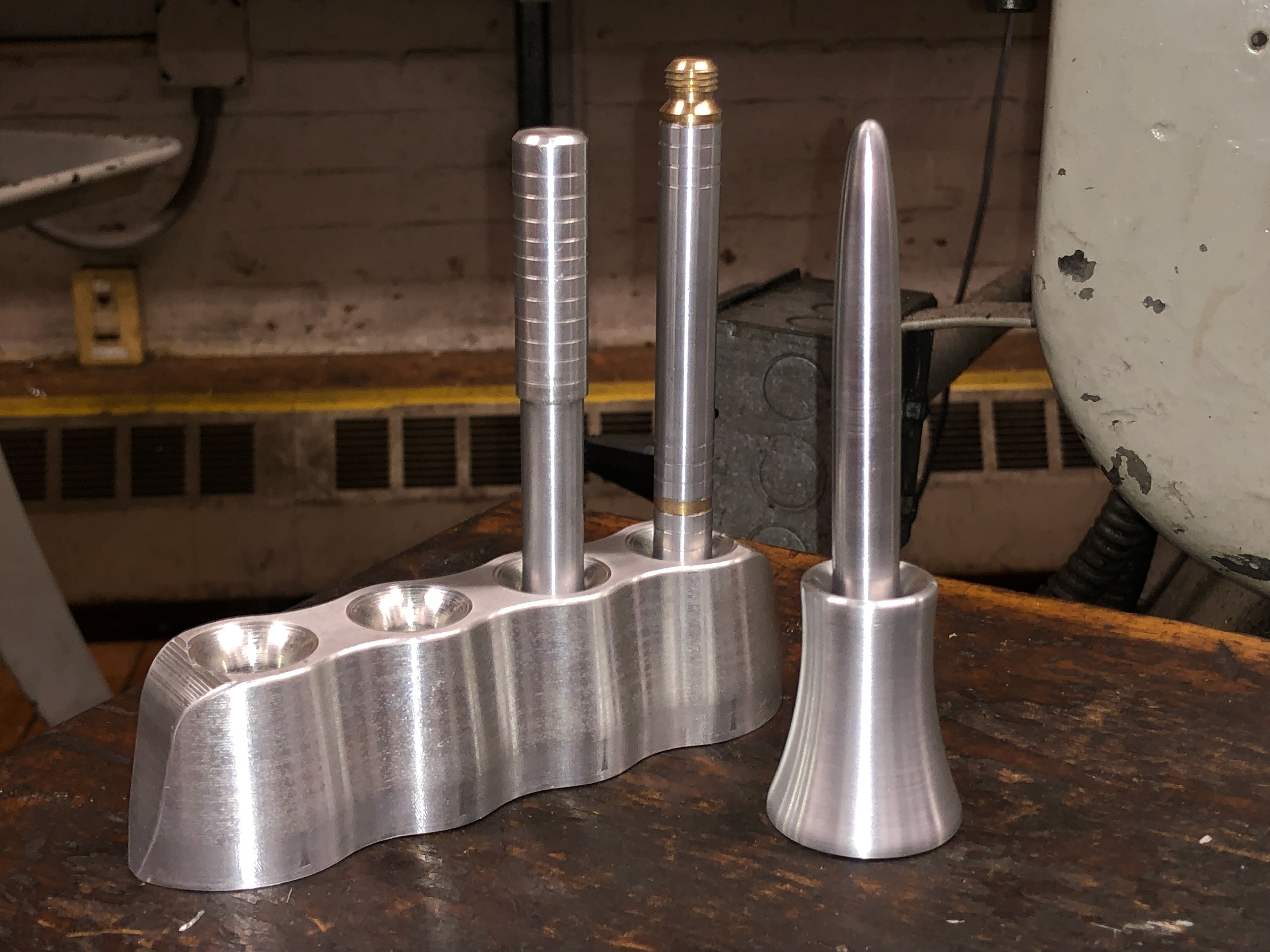
Below, the evolution of my designs as well as the improvement of my skills can be seen through the 3 pen projects and the 2 pen holders.
Pen #1
This pen was made as a prototype, mainly to experiment with the specific metal lathe processes of making a pen and pinpointing the inner dimensions I need to fit the cartridge.
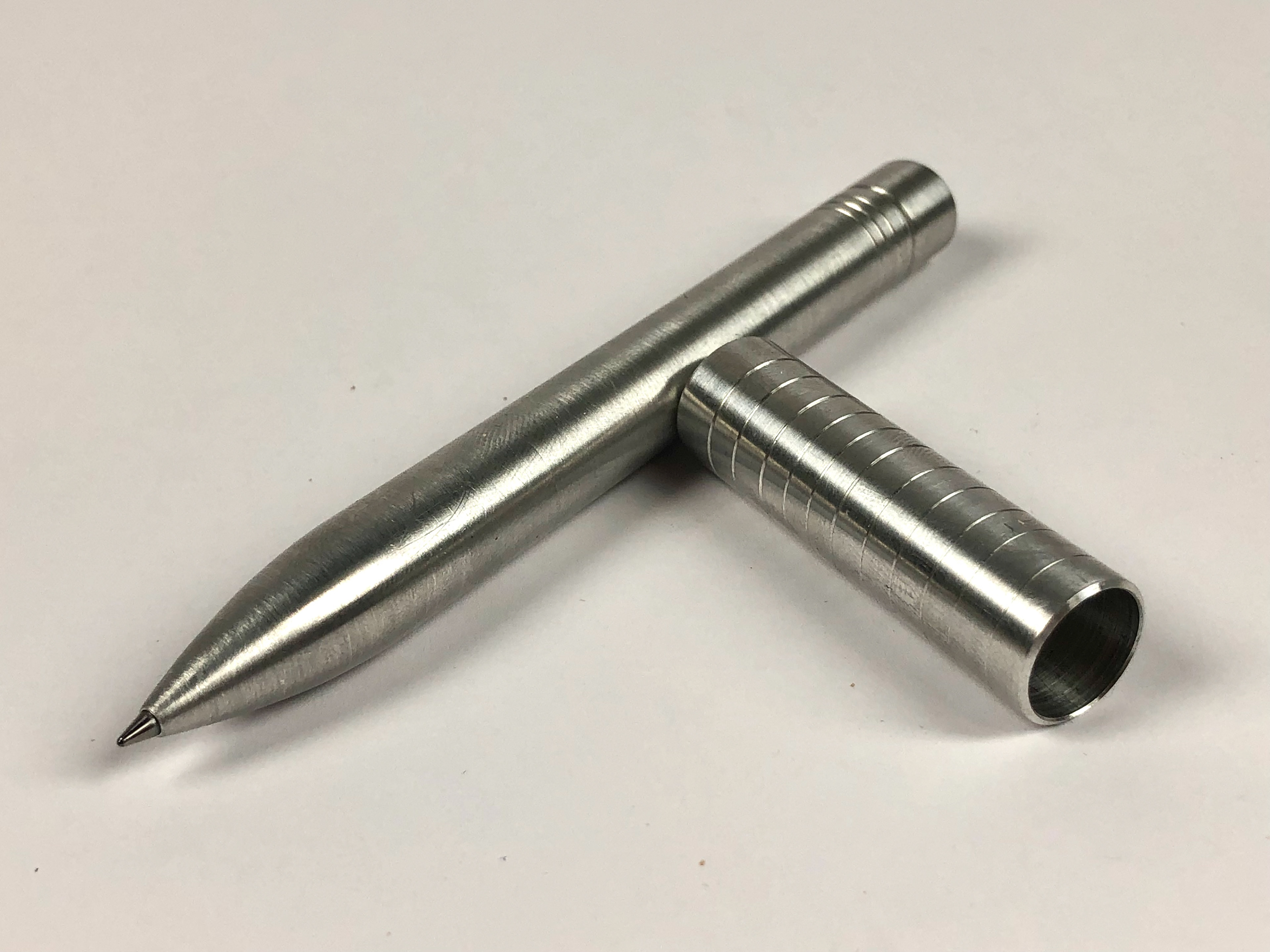
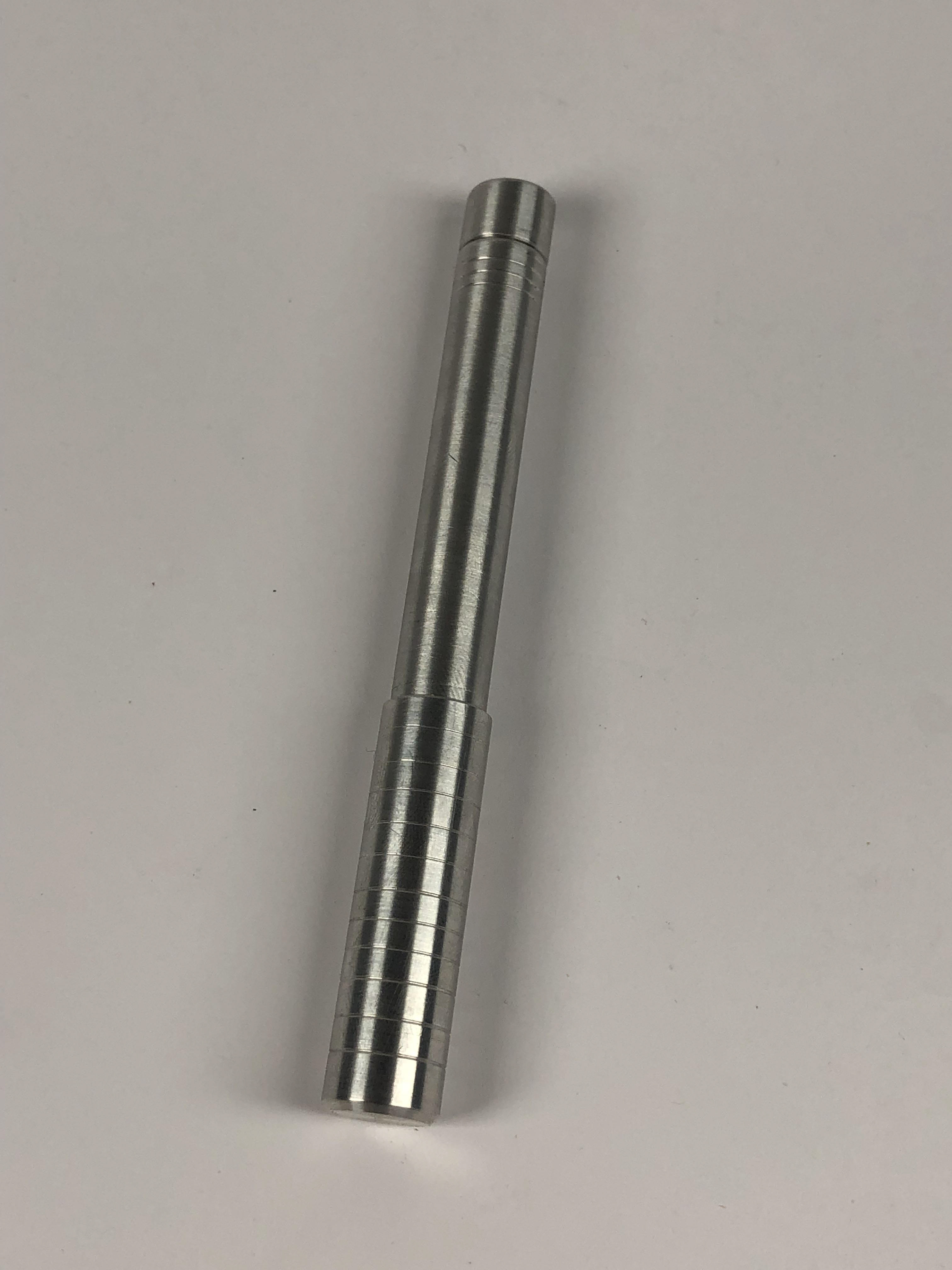
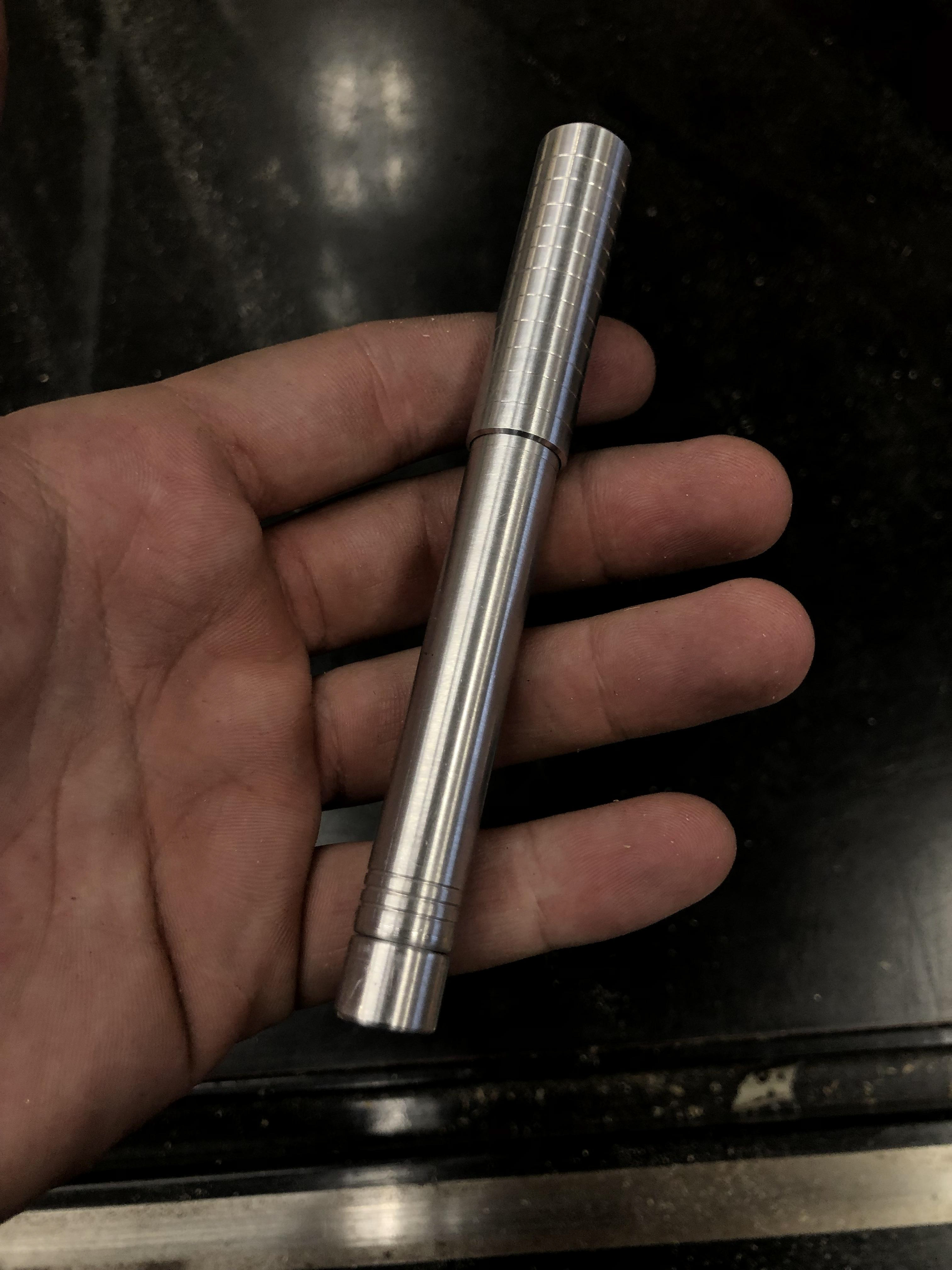

Pen #2
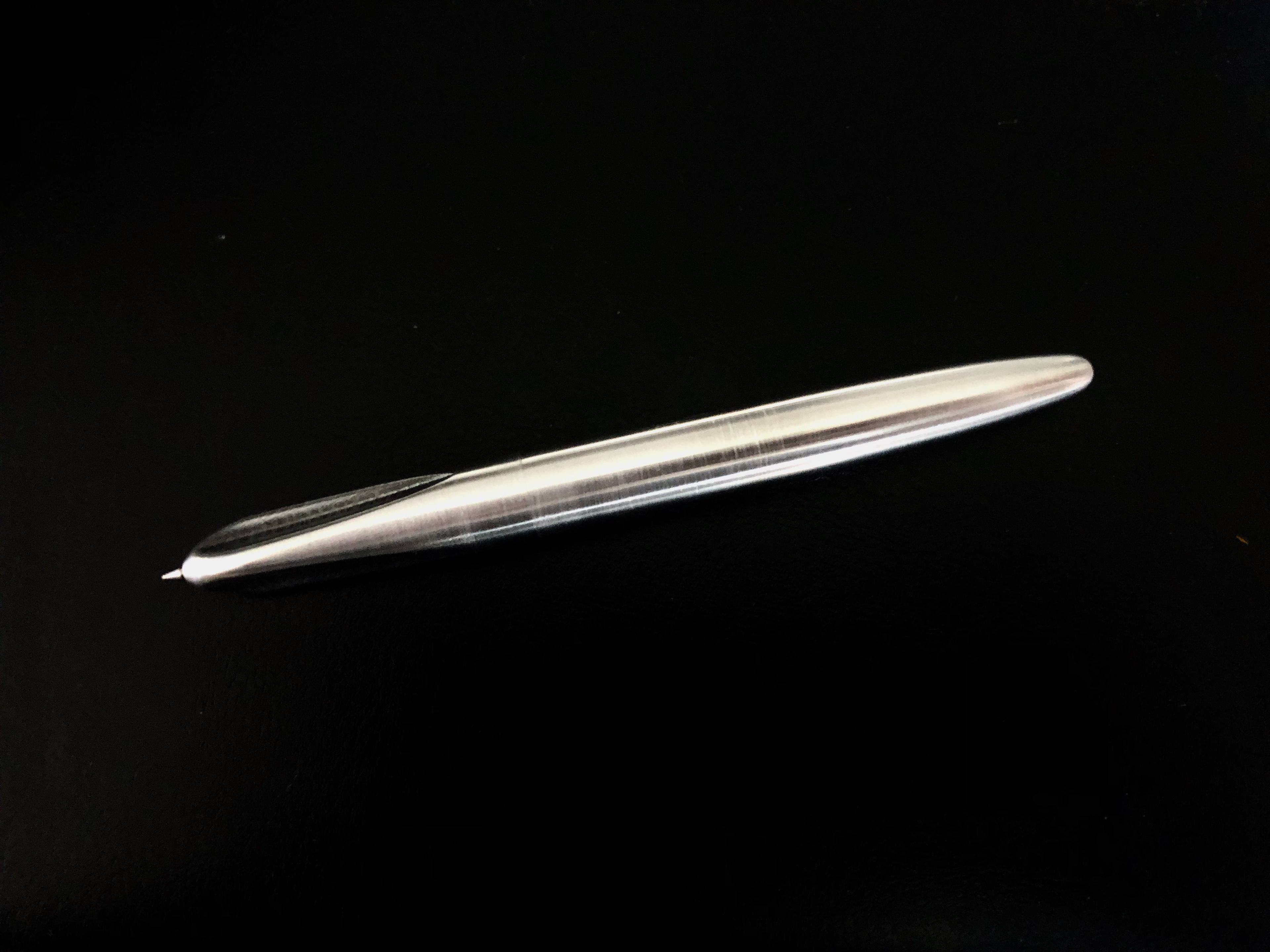
Pen #2 was born from the idea of further reducing the parts required to make a pen. After experimenting with different drilling techniques and achieving the precision required for the main body, I was able to get rid of the back cap screw.
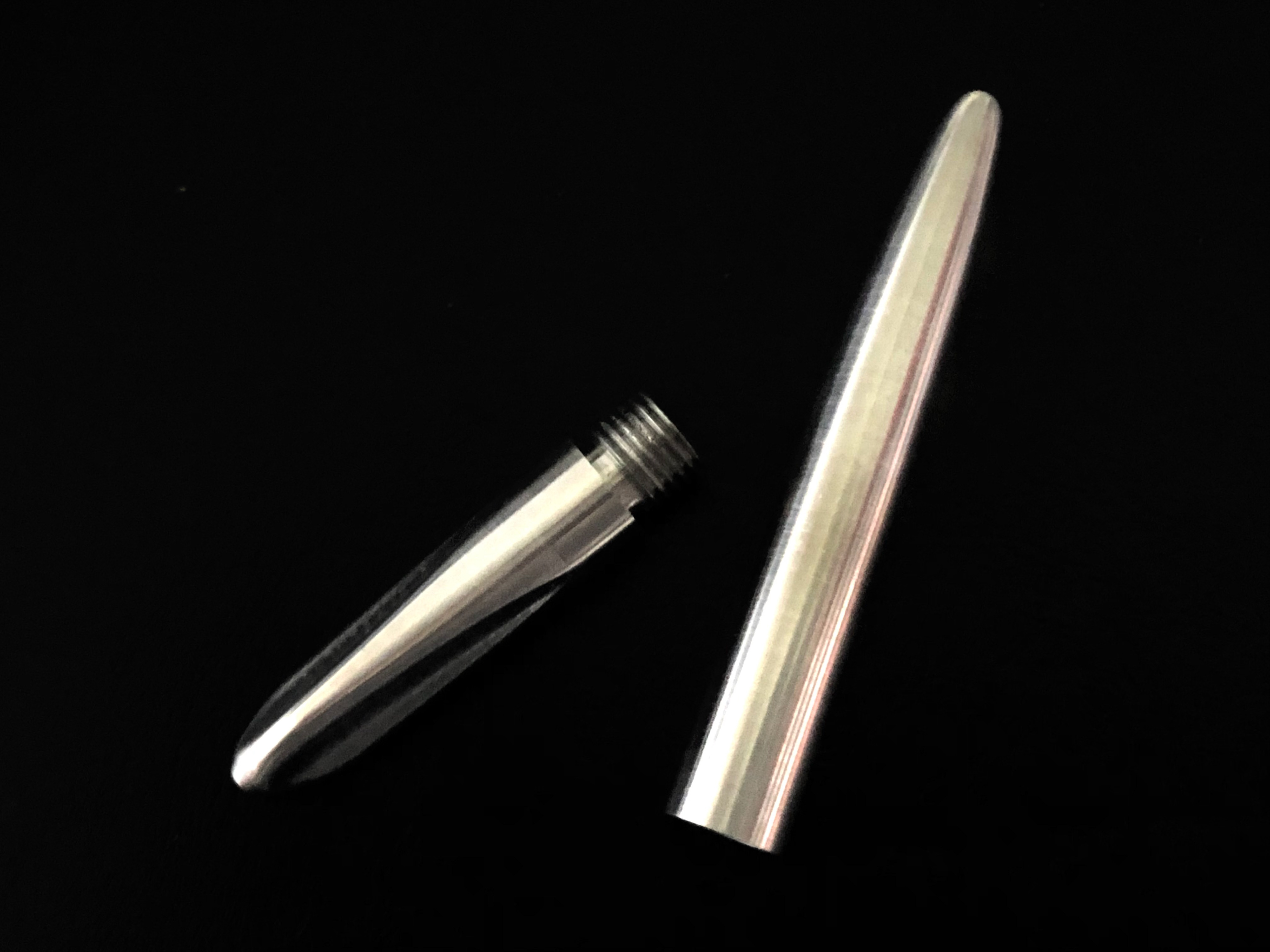
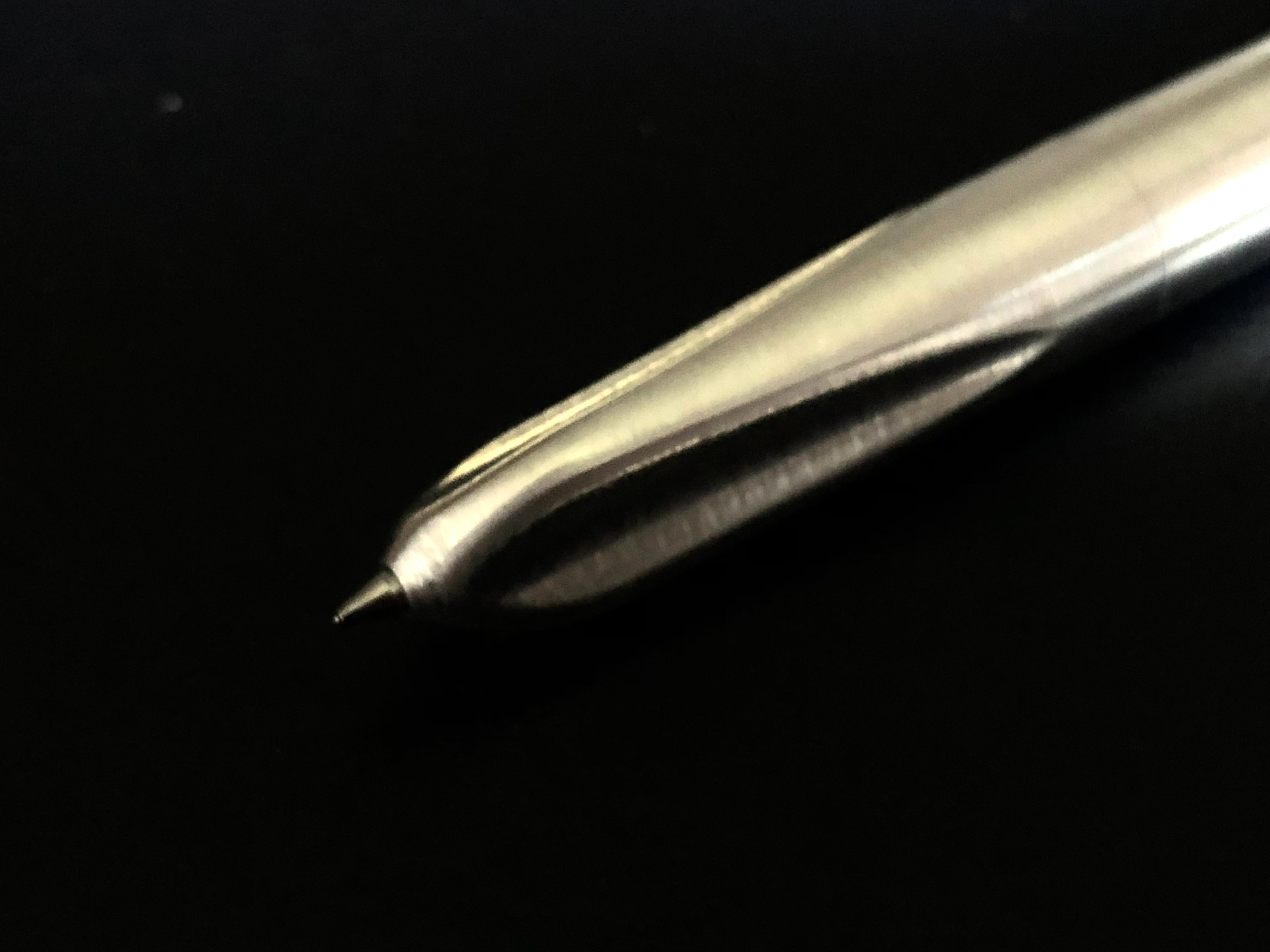
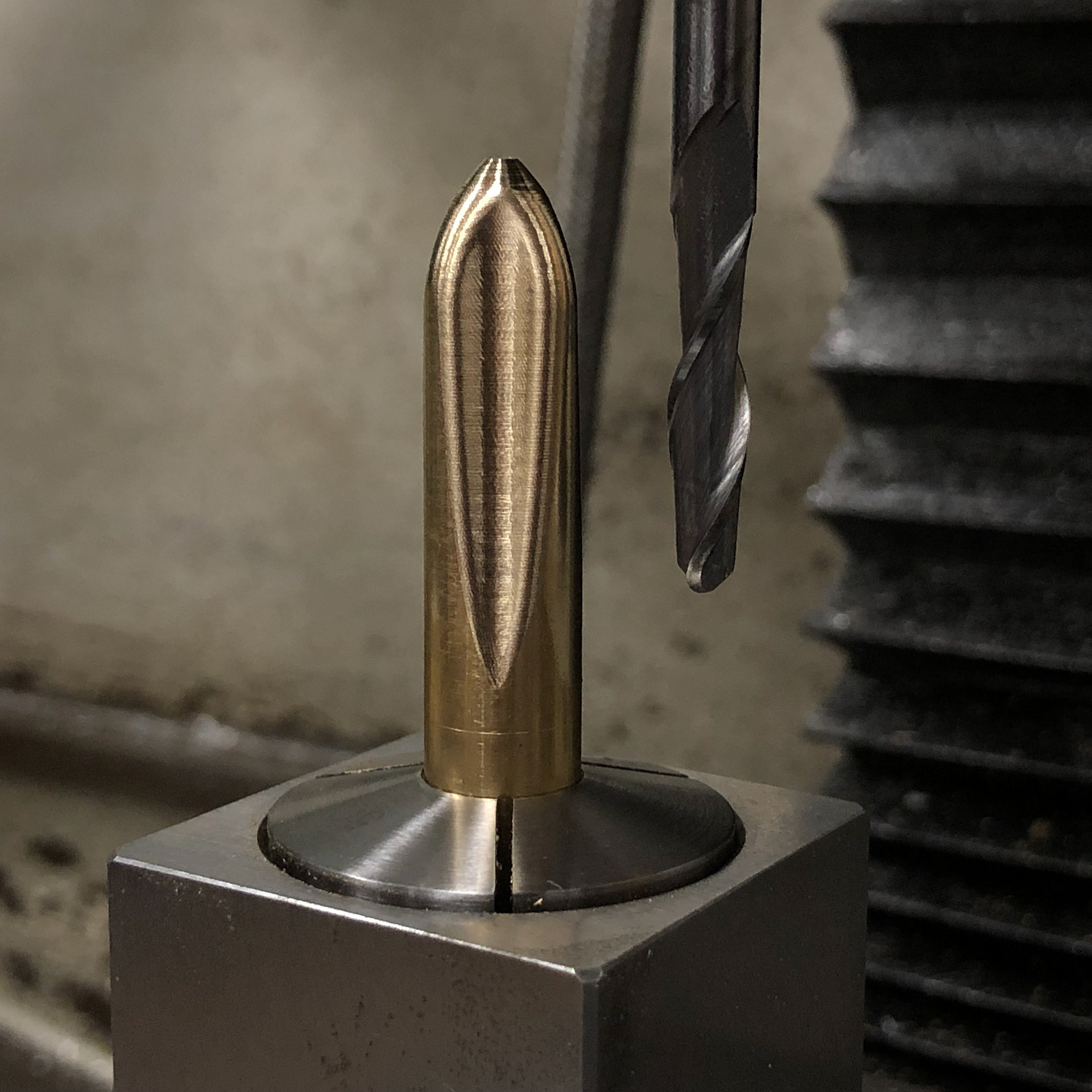
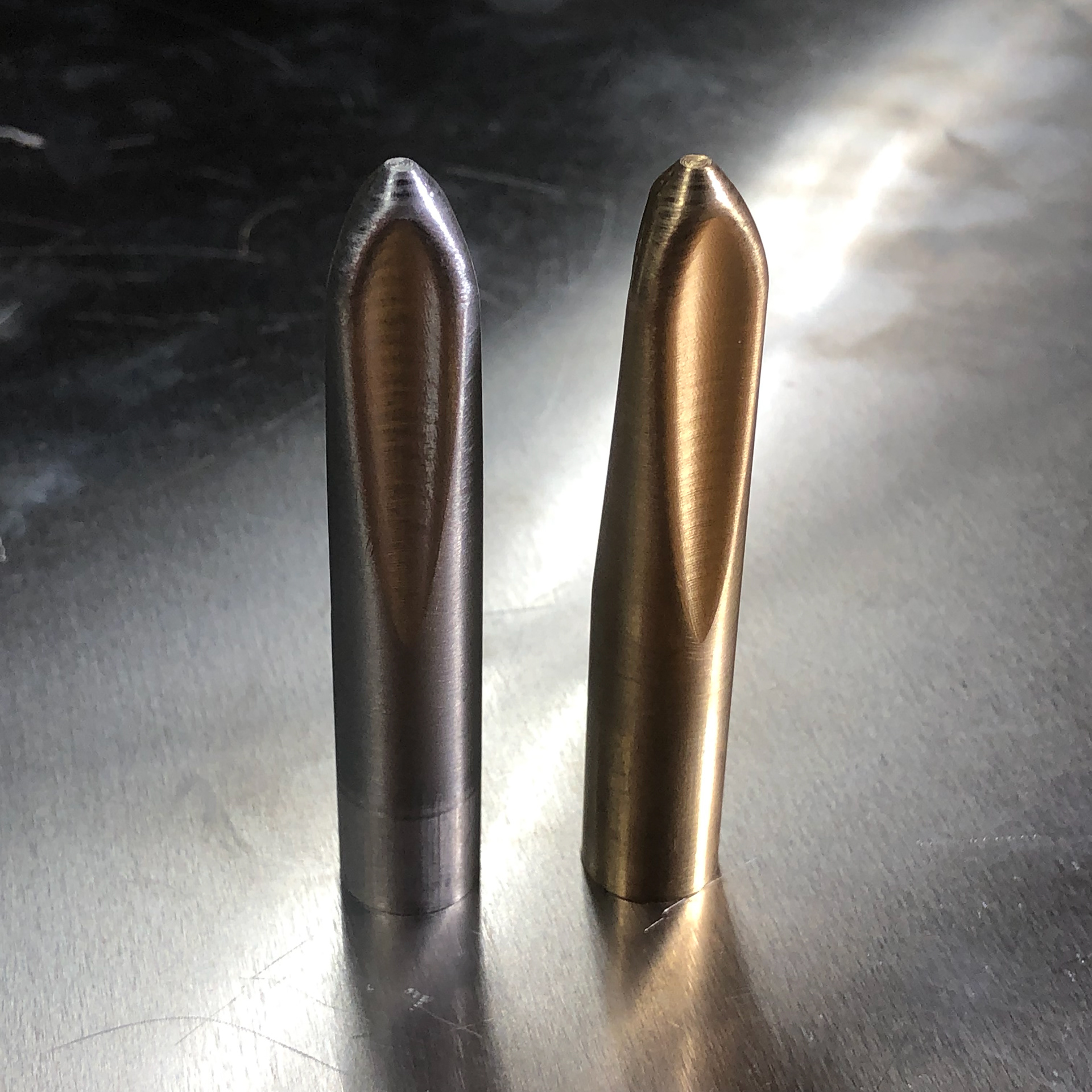
The parts seen above were made using a CNC Mill. I wanted to make a special grip for this pen to not only have it be a circular profile, resulting in a more comfortable ergonomic grip. I completed one aluminum and one brass version.
Pen #3
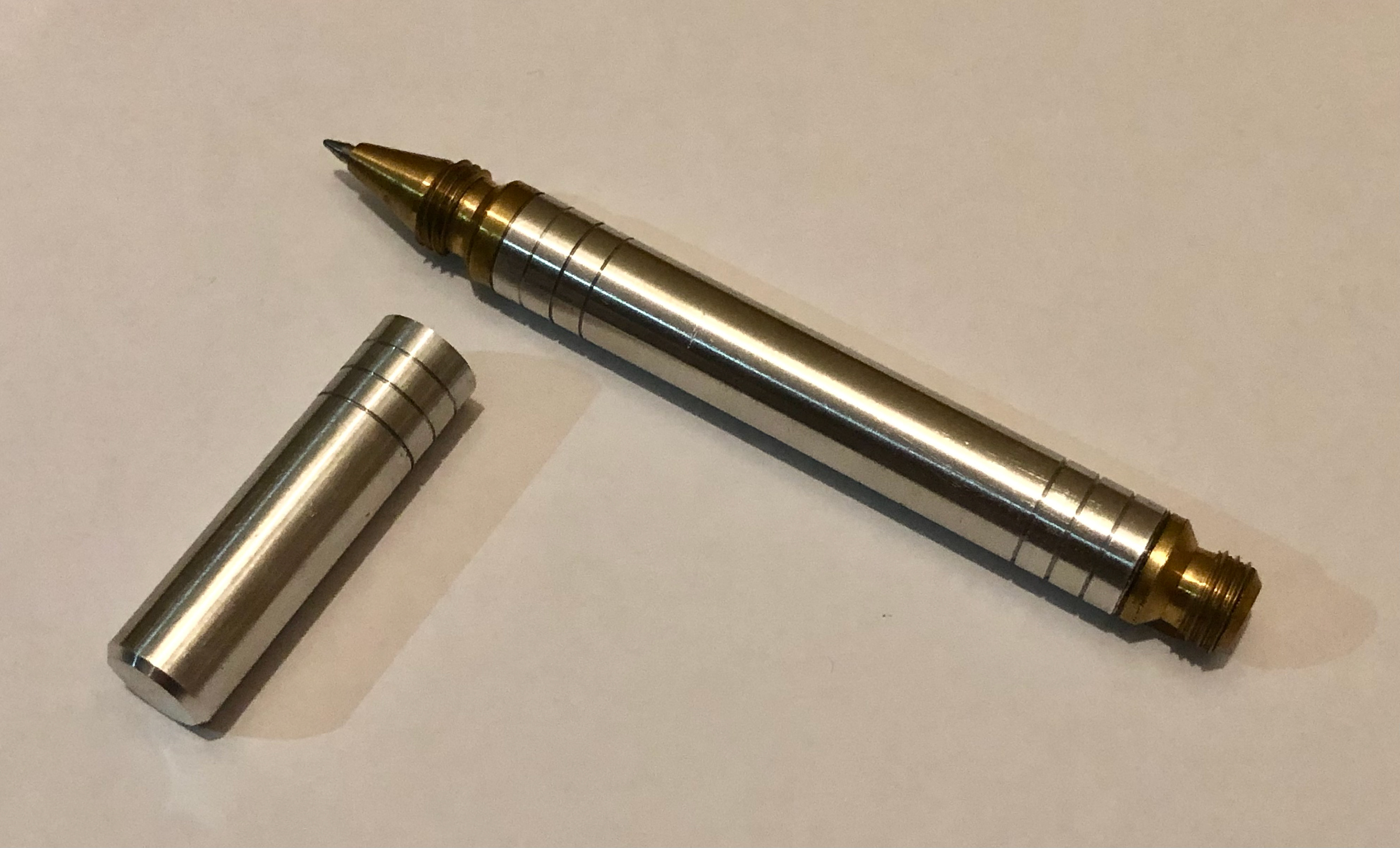
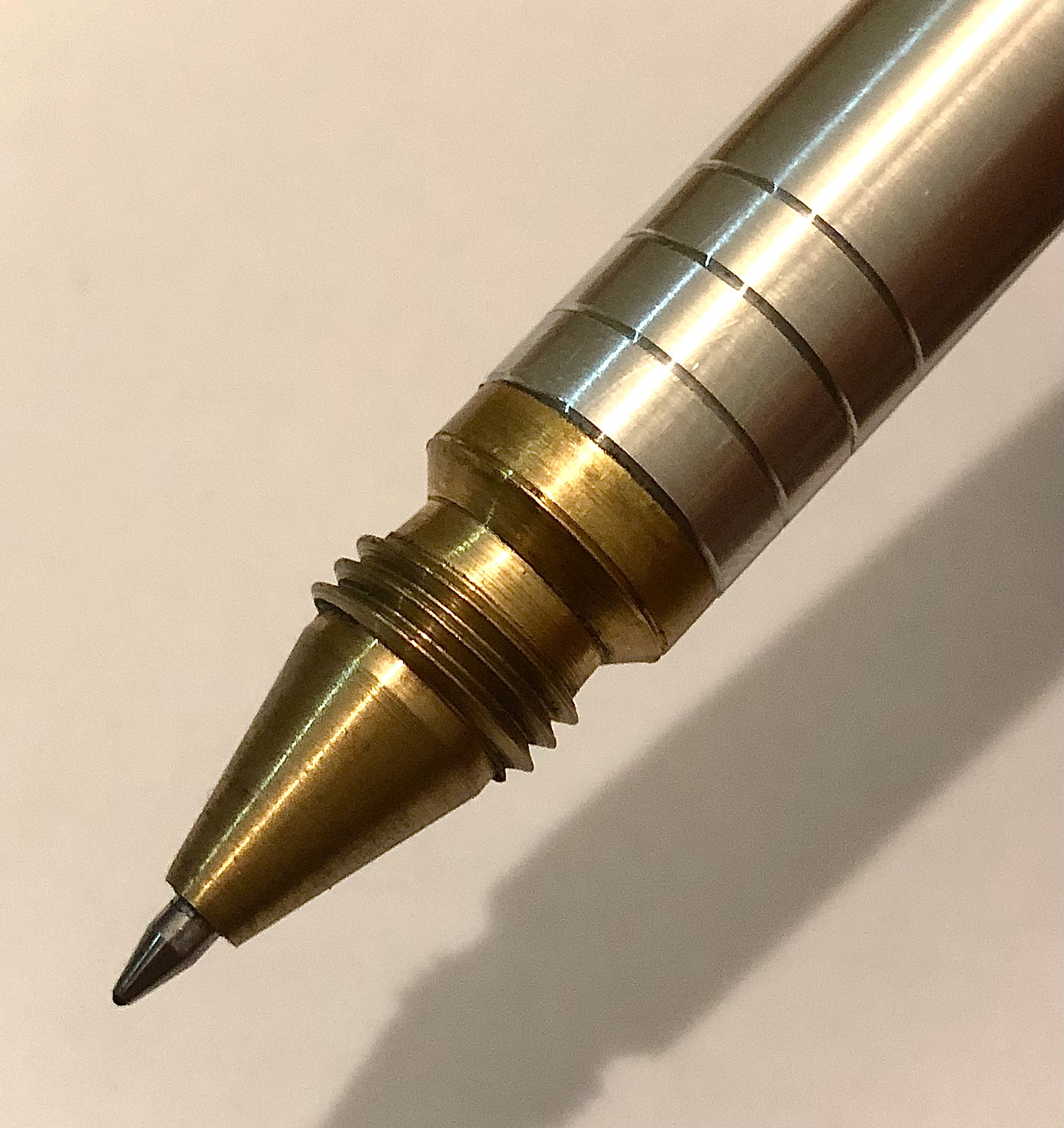
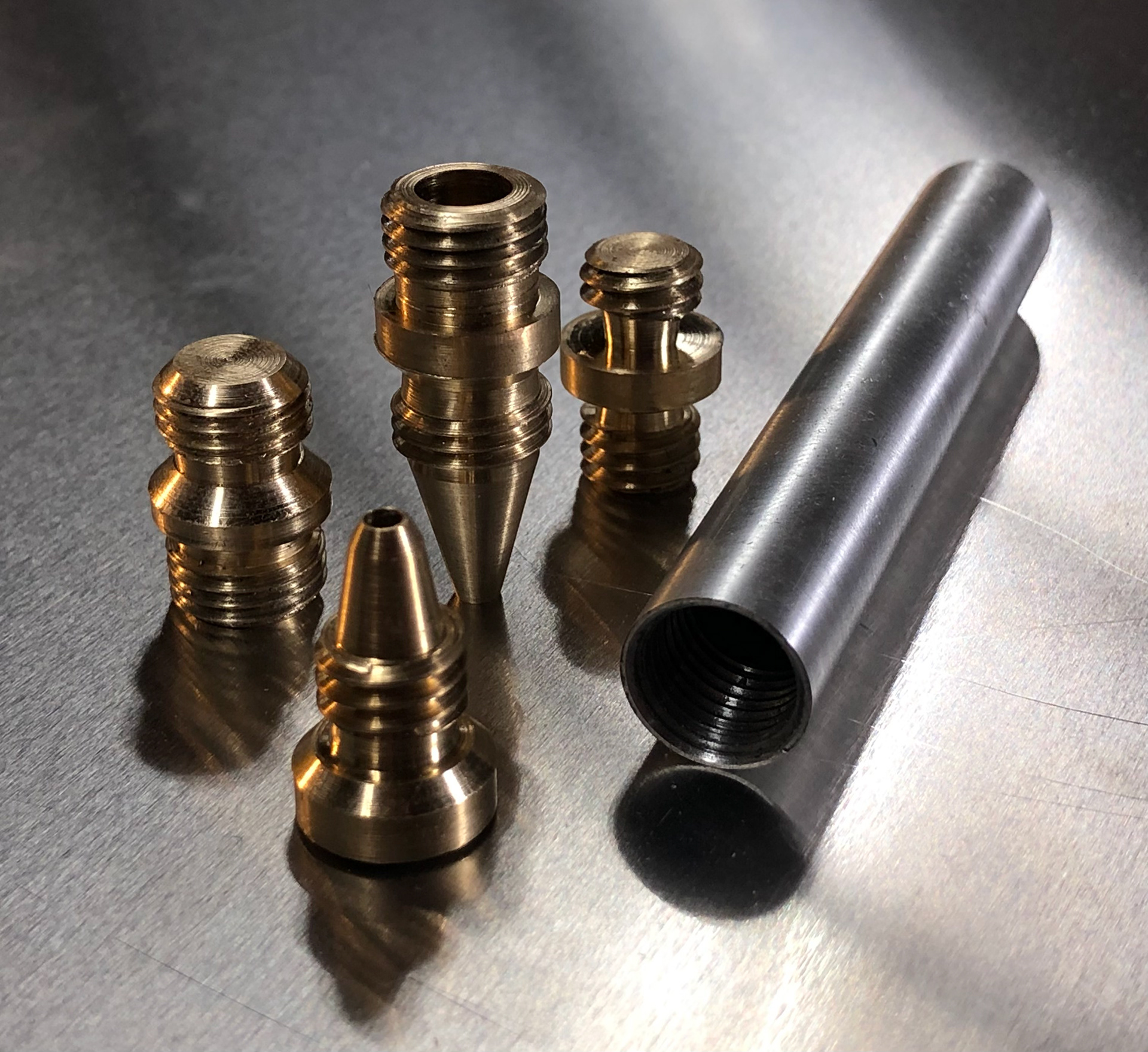
Pen #3 was my final design for my Metal Machining class and it was based on my past pen machining experiences (and mistakes!)
Some of the main differences included using brass and experimenting with mechanically connecting different metals, as well as threading the detachable parts to for the pen cap. Pen #1's cap was prone to wearing off because it relied on being a friction fit for a soft metal. The threads make the parts a lot more tolerant wearing off over time.
To finish off the project, I also CNC machined a pen holder to store all of my pens in. There is always room for improvement so I added a symbolic 4th hole as a signifier of my future iterations!
The tabs in the bottom were later cleaned and fly-cut to make it smooth.
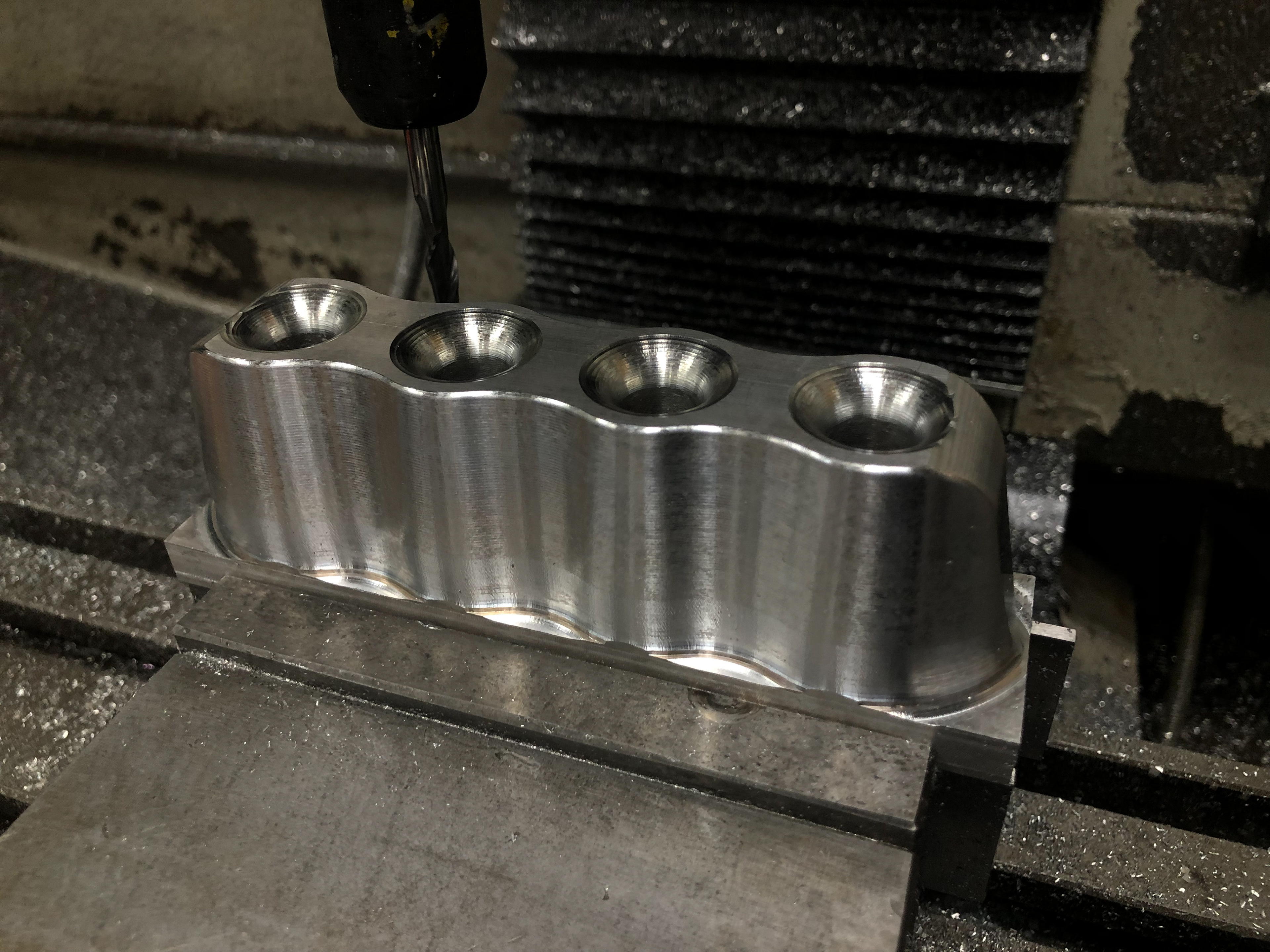